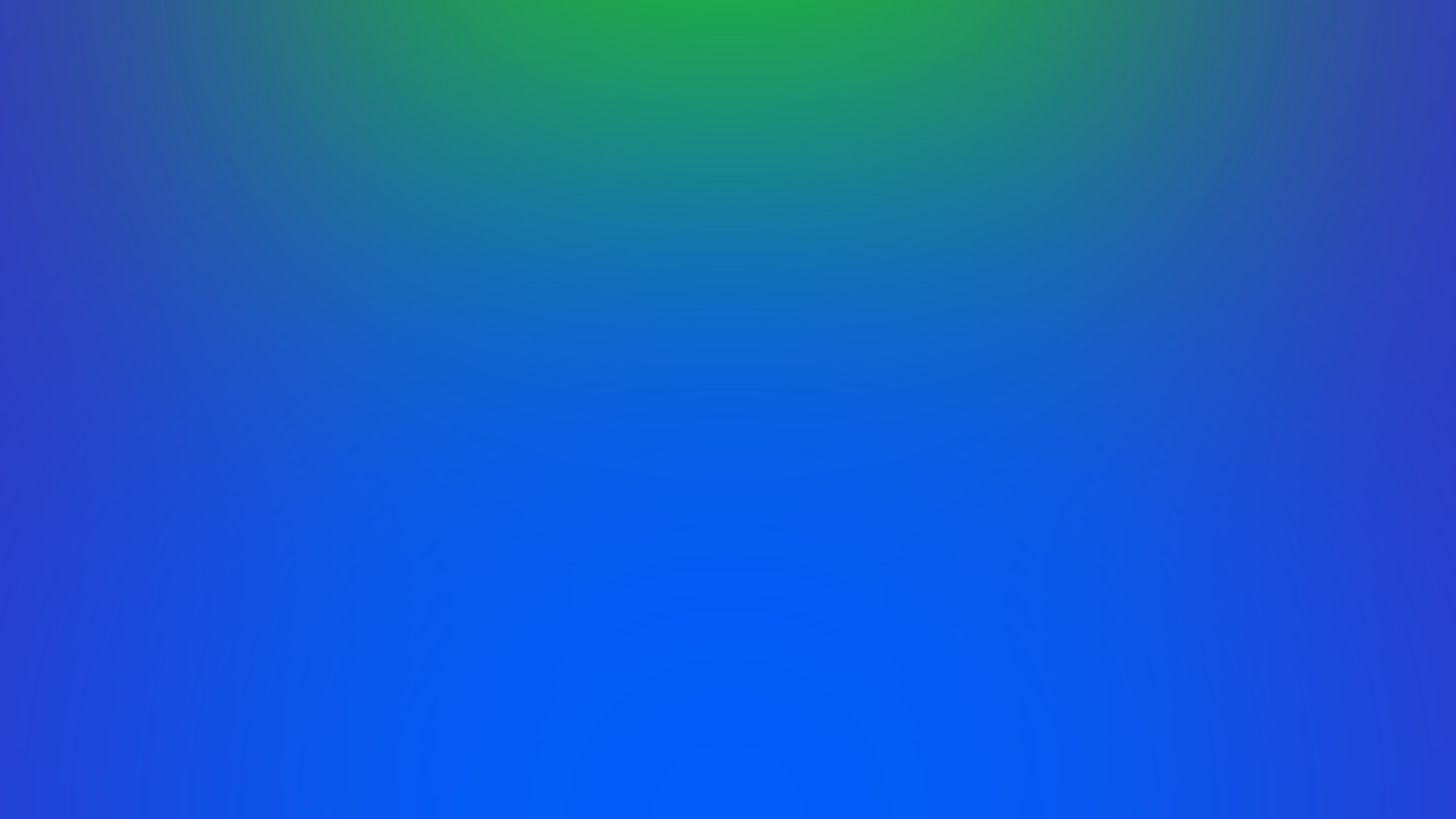
Next Generation Work Ability Management Platform
Aino provides data-driven insights to improve work ability,
well-being and productivity to build high performing organizations.
Reduce sickness absences by 20 - 60%
Understand the true reasons of sickness absence and mental health challenges
Systematize and automate actions for line managers to offer preventative support for employees
Boost productivity, social sustainability and be compliant
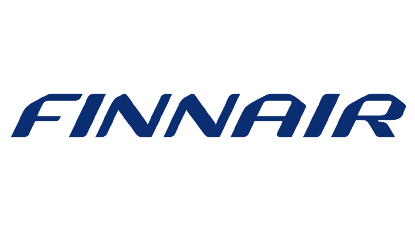
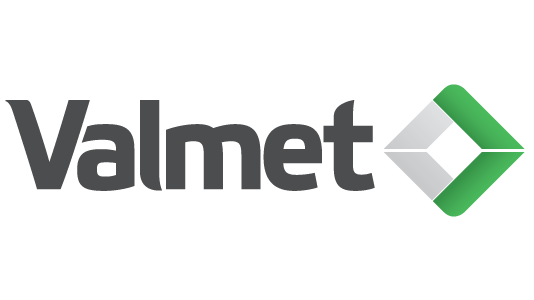
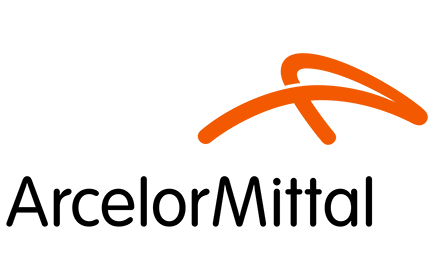
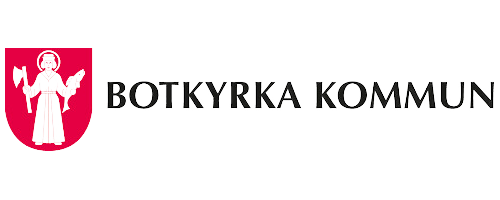
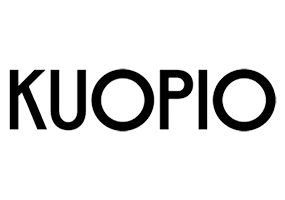
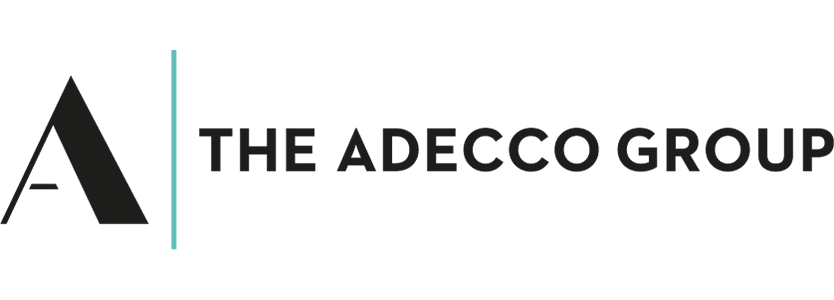
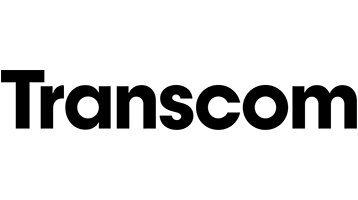
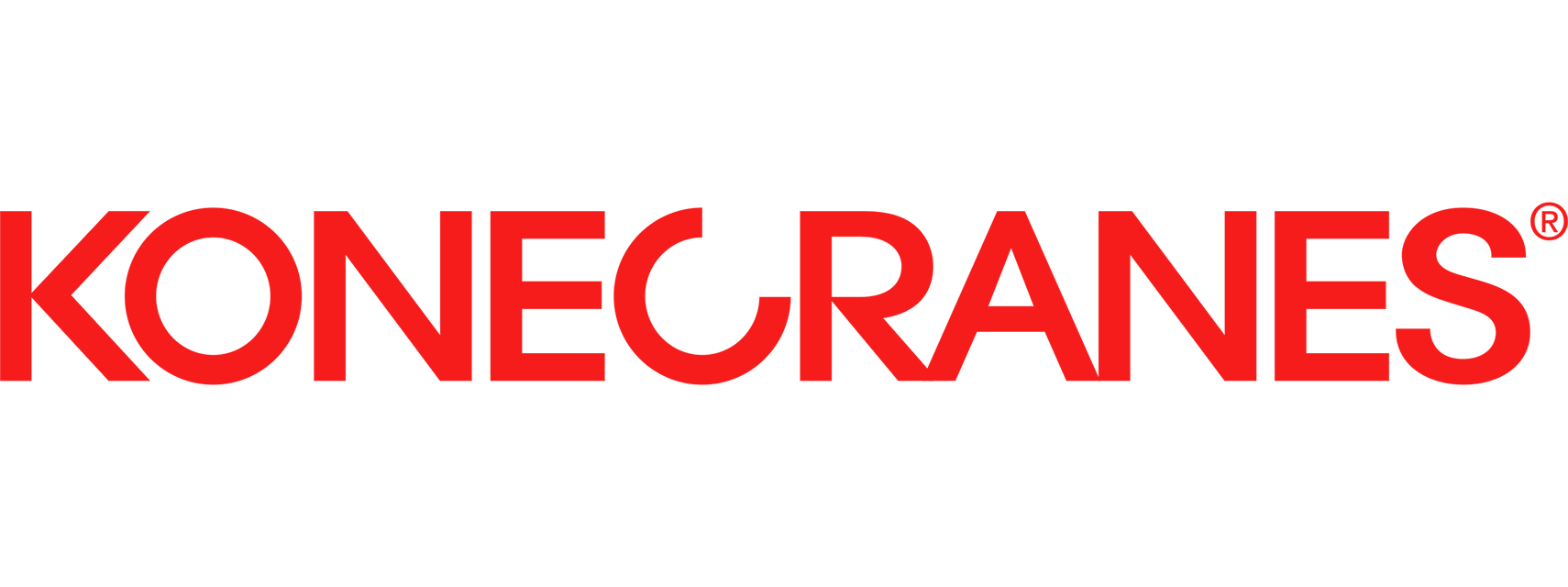
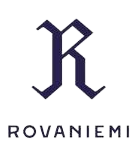
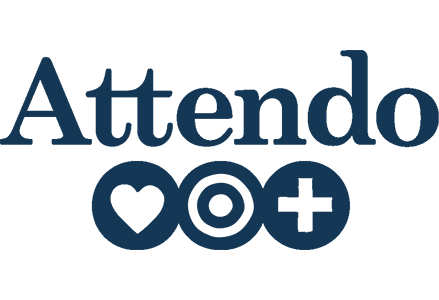
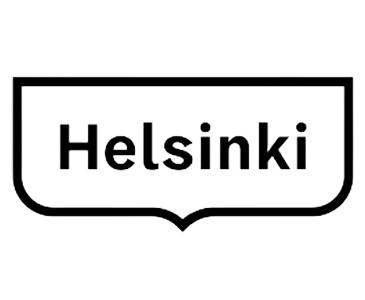
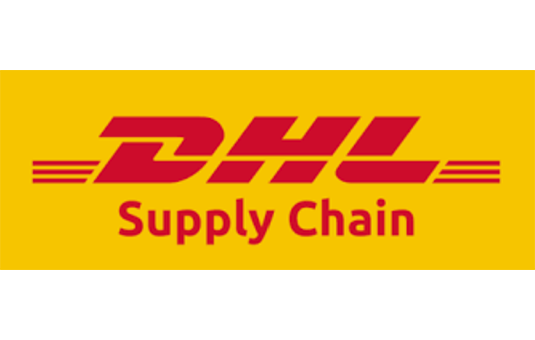
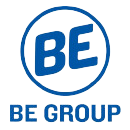
What our customers say
Aino highlights!
Why Aino?
For employees
Early support from qualitative conversations, improved job satisfaction, well-being, feeling of inclusion, value and confirmation.
For line management
Guidance for early support conversations, centralized data and instructions, automated triggers, proactive actions.
For HR
Reduced manual work for reporting, best practice, ready made processes, local and global integration and compliance.
For top management
Insights to root causes for absence, automated KPI’s and metric tracking, substancial cost savings, GDPR compliance. Enabling a shift from reactive to strategic leadership.
A Global Platform
We connect the dots!
Our research based global platform is designed to understand the true root cause of your employees’ absence, to identify and address underlying causes early and prevent them forward.
We digitalize all work ability related efforts and offer managers the tools they need to provide the right support to the right employee at the right time, bringing your organization to optimal operation.
Private and public customers using Aino develop a modern and responsive leadership, while becoming socially sustainable, productive and attractive. A win-win-win, for the employees, line managers, HR and top management.
Customer story with The Adecco Group
Hear more about the successful implementation of Aino in The Adecco Group.
9 of 10 employees value the systematic support enabled by the platform
Improved financial result
Increased customer satisfaction
A more sustainable work environment
Aino in 90 seconds
Learn what the Aino platform can do for your organization.